3D printing refers to several manufacturing technologies that build parts layer by layer. They differ in the way they produce plastic and metal parts as well as in the materials they use, the surface finish, the durability, and the speed and cost of their manufacturing.
3D printing includes several types, including:
- Stereolithography (SLA)
- Laser sintering (SLS)
- Modeling of fused depositions (FDM)
- Digital Light Processing (DLP)
- Fusion of multiple jets (MJF)
- PolyJet
- Laser Direct Metal Sintering (DMLS)
- Melting of electron beams (EBM)
Understanding the strengths and weaknesses of each 3D printing process, and mapping those attributes to the needs of your product development project, is crucial to selecting the right process for your application. We will first discuss how 3D printing fits into the product development cycle, and then explore common types of 3D printing technologies and their advantages.
Rapid Prototyping with 3D Printing
Prototyping is the most common use for 3D printing. Its ability to manufacture a single part quickly enables product developers to validate and share ideas in a cost-effective way. The purpose of your prototype will determine which 3D printing Gosford technology will be most effective. A range of prototypes can be built using additive manufacturing, from simple physical models to functional parts.
Even though 3D printing is almost synonymous with rapid prototyping, there are situations in which it is a viable production method. Low volumes and complex geometries are typical for these applications. Components for aerospace and medical applications are often ideal candidates for production 3D printing since they often match the criteria previously described.
Considerations for 3D Printing
As with most things in life, deciding on a 3D printing process is not an easy decision. We typically use five criteria to determine the right technology for our customers when evaluating their 3D printing options:
- Budget
- Mechanical requirements
- Cosmetic appearance
- Material selection
- Geometry
After an SLS build is complete, the technician removes the part from the powder bed, brushes off excess material, and then bead blasts the part.
Processes for 3D Printing Polymer
In this article, we will outline some common plastic 3D printing processes and discuss when each delivers the most value to designers, engineers, and product developers.
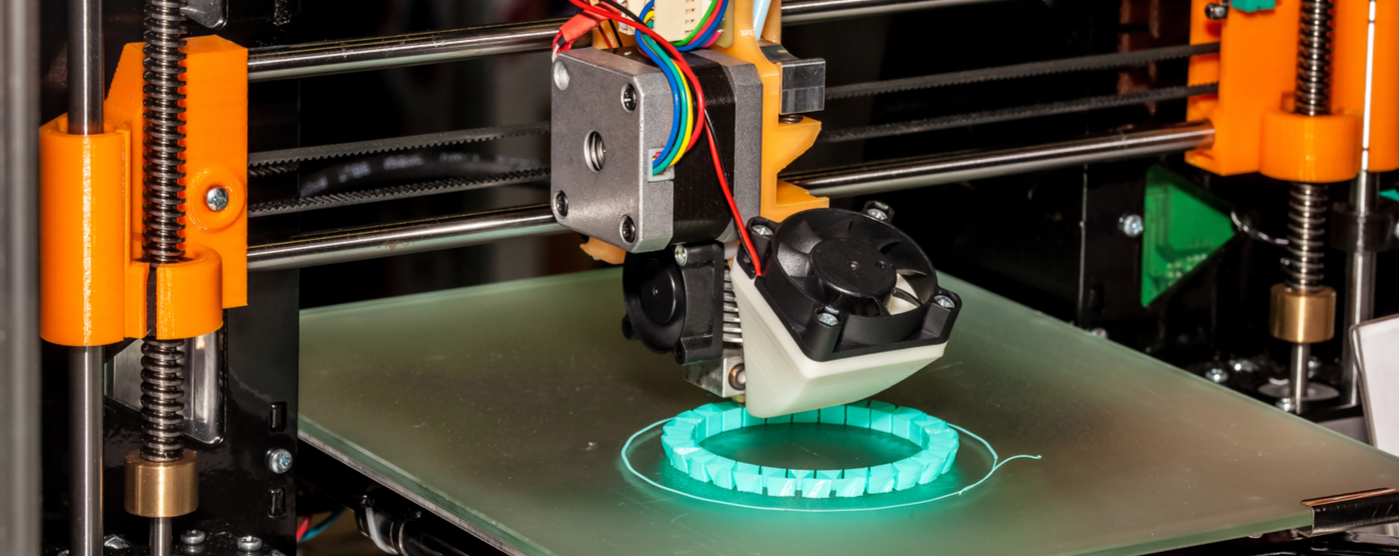
Stereolithography (SLA)
Original 3D printing method is stereolithography (SLA). A SLA printer produces parts with high levels of detail, smooth surfaces, and tight tolerances. The quality of surface finishes on SLA parts can not only look good, but also help with the part’s functionality, such as testing the fit of an assembly. Anatomical models and microfluidics are some of its most common applications in the medical industry. Our SLA parts are printed on Vipers, ProJets, and iPros 3D printers manufactured by 3D Systems.
Laser selective sintering (SLS)
SLS is a method of solidifying nylon-based powders by melting them together. A SLS part is made of real thermoplastic material, which is durable, suitable for functional testing, and can support living hinges and snap-fits. SL parts are stronger than SL, but their surface finishes are rougher. It can nest multiple parts into a single build because SLS doesn’t require support structures, which makes it more suitable for larger part quantities that other 3D printing processes cannot handle. Injection-molded parts are often prototyped using SLS. 3D Systems developed the sPro140 machines we use for SLS printing.
PolyJet
There’s a twist to PolyJet, another plastic 3D printing process. This method can produce parts with multiple properties, including color and material. The technology can be used to prototype elastomeric or overmolded parts. Our recommendation is to stick with SL or SLS if your design consists of a single, rigid plastic. PolyJet can save you the cost of tooling if you’re prototyping an overmolding or silicone rubber design. Your design can be iterated and validated faster and more efficiently.